Manufacturing is a central part of industrial production. Manufacturers must improve productivity in manufacturing to thrive in the market and reduce costs.
There are numerous ways to improve the manufacturing process, but many companies fail to use them effectively. In this article, we will explain options on how companies can increase productivity in manufacturing.
To improve productivity in manufacturing, companies must implement a comprehensive and all-inclusive strategy. Successful strategies often include training or coaching solutions for employees and managers.
Employee development
Training employees is essential, as they must have the skills to use new technologies effectively. Good training can also help increase productivity by enabling employees to work more efficiently. Training efforts should, among others, focus on leadership development.
Indeed, leadership development solutions can boost company success using the assets at hand. One-on-one business coaching, in particular, is highly effective in enhancing leadership productivity and, in turn, team performance. Through the targeted use of business coaching, otherwise unattainable insights come to light. Such insights help in identifying and implementing new technologies relevant to the market. Business coaching sessions also reduce internal resistance to such change.
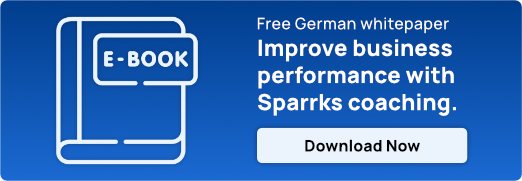
Latest technologies
Companies must choose the right technologies relevant to their specific needs and processes. Below we have listed four innovative technologies that can enable companies to increase productivity in manufacturing.
Automation
Automation has become increasingly prevalent in manufacturing and for good reason. It can lead to significant improvements in productivity, efficiency, and accuracy. Also, automation can help streamline processes, reduce errors, and optimize workflow. For example, productivity increased by up to 15 % due to industrial robotics in Germany between 2010 and 2015, a study published by the Centre for European Economic Research (ZEW). This report also indicated that productivity gains from automation are mainly due to the substitution of manual labor for machinery, which can perform repetitive tasks with greater precision. It confirmed that automation helps streamline processes, reduce errors, and optimize workflow.
Automation can help increase productivity and efficiency by reducing labor and improving product accuracy and quality. It allows companies to produce more products in less time, reducing costs. Also, it can help companies increase their market share by providing faster delivery times and a better customer experience.
And that's not all! According to a study by the International Journal of Occupation and Environmental Health, adapting automation facilitates progress in workplace safety by minimizing risks and simplifying workflows. That leads to fewer injuries on the job, particularly for the most dangerous and labor-intensive tasks. Furthermore, a Deloitte study found that automation helps companies increase their market share by providing faster delivery times and a better customer experience.
Data Analytics
Data analytics is a powerful tool that can help manufacturers improve productivity in varying ways. A study by the National Institute of Standards and Technology found that manufacturers who implemented data analytics techniques experienced a 30% reduction in defects and a 25% increase in productivity. Additionally, data analytics can help manufacturers predict demand and optimize inventory levels, reducing waste and ensuring the efficient use of production resources.
Data analytics is a very effective way to improve productivity in manufacturing. It is one of the key trends in the modern manufacturing world. By analyzing large amounts of data, managers can optimize manufacturing processes.
According to a study conducted by McKinsey & Company, data analytics can help manufacturing companies reduce maintenance costs by up to 40% and downtime by up to 50%. Furthermore, an additional study by PwC found that manufacturers that use data analytics can improve their overall equipment effectiveness (OEE) by up to 20%. In short, data analytics effectively improves productivity in manufacturing by providing an opportunity to optimize manufacturing processes, giving companies insights to make better decisions, and reducing production costs.
Machine learning
Machine learning is a type of artificial intelligence that involves training computer algorithms to learn from and make predictions or decisions based on data inputs without being explicitly programmed. Machine learning algorithms analyze production data and derive insights that can optimize manufacturing processes, improve product quality, and increase overall productivity.
Machine learning is an innovative technology used in many fields to automate processes and increase productivity. With the help of machine learning, companies can optimize processes by collecting and analyzing data. Along with data analytics, the quality of products improves by identifying and solving problems at an early stage.
According to a survey conducted by Deloitte, 68% of manufacturers have already implemented or plan to implement machine learning technology in their operations. One area in which machine learning has been particularly effective is predictive maintenance. A study by PwC found that manufacturers who implement predictive maintenance through machine learning technology can reduce maintenance costs by up to 30% and increase equipment uptime by up to 20%. Machine learning algorithms predict equipment failure upfront by analyzing machinery-specific data (such as temperature, vibration, and pressure sensors). That allows corrective action before any damage occurs.
Another application of machine learning in manufacturing is quality control. By analyzing production data, machine learning algorithms can identify patterns and deviations from the norm that might indicate quality issues. That can help manufacturers catch defects earlier in production, improving product quality and reducing waste. An interesting research on this issue found that companies implementing machine learning in their quality control processes can reduce defects by up to 50%.
Mobile technologies
Mobile technologies in manufacturing can simplify, automate and optimize production. Most notably, these include mobile robots capable of performing tasks such as gripping, lifting, moving, and transporting materials. For instance, mobile robots that lift materials can automate tasks previously performed manually by human workers. This results in fewer delays, increased output, and better product quality. A study published in the International Journal of Advanced Manufacturing Technology found that autonomous mobile robots for material handling increased productivity by up to 50% in a manufacturing simulation.
Mobile technologies in manufacturing can simplify, automate and optimize production. Most notably, these include mobile robots capable of performing tasks such as gripping, lifting, moving, and transporting materials. The data collected through mobile technologies ultimately serves managers to monitor and control processes.
Other mobile technologies used in manufacturing include wearable devices such as smartphones and tablets. Such devices provide employees with access to real-time production data, which enables them to monitor processes, identify bottlenecks, and make more informed decisions. Additionally, wearable devices can assist in various tasks such as inventory management, quality control, and remote troubleshooting. That improves employee mobility across the manufacturing facility, allowing quicker response times and improved decision-making. Also, the data collected from wearable devices can help managers streamline production scheduling, track performance metrics, and optimize workflows.
Recap
The four technologies mentioned above can significantly help optimize processes and improve product quality. They can also help reduce costs and increase the company's competitiveness.
Therefore, companies must use these technologies to increase productivity in manufacturing. Companies should also select the right partners to implement the technology into their manufacturing processes.
Culture of continuous improvement
In modern manufacturing, a culture of continuous improvement is essential to increase productivity and efficiency. This approach aims to evaluate, analyze and optimize existing processes to create value for customers and the business. Companies can improve their competitive advantage by constantly finding new ways to optimize the manufacturing process. Such constant optimization allows for producing faster, more cost-effective, and more efficient products.
To establish a culture of continuous improvement, companies must first create a clear vision for the future and foster a culture of growth and innovation. Such a vision requires involving employees at all levels in generating new ideas and processes. This approach also encourages all employees to provide feedback to improve processes and drive innovation. Implementing innovation management for employees is therefore highly recommended.
Furthermore, companies need to implement a structured and systematic method for continuous improvement. Such a method includes identifying weaknesses in existing processes and developing solutions to address them. It requires understanding the processes and constant monitoring so that updates hold on effectively.
In conclusion, organizations must create a culture where all stakeholders are accountable for achieving goals. It requires a culture of engagement and collaboration where all employees are interested in improving productivity and efficiency. Such behavior enables companies to become more competitive and create added value for customers and the company.
Conclusion
There are many ways to improve productivity in manufacturing. However, companies need to develop a strategy that encompasses all organizational levels. Managers must select the right technologies and train employees to use such technologies effectively. Also, to increase productivity in manufacturing, companies must create a culture of perpetual improvement. When companies apply these strategies, they can significantly increase productivity in manufacturing and improve their competitiveness.
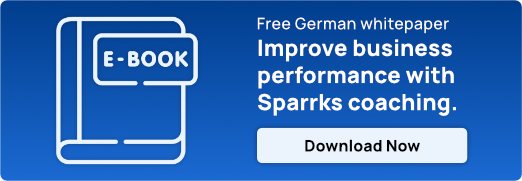
FAQ: Improve productivity in manufacturing
How to measure productivity in manufacturing?
Measuring productivity varies across industries, but the principle remains the same: divide the output produced (commonly measured in the number of produced goods and services or sales made) by the inputs used in the production process (input examples being labor hours, capital, and natural resources).
What are some recent examples of successful innovation technologies in manufacturing?
Recent technological innovations in manufacturing include artificial intelligence (AI), industrial robotics, additive manufacturing (CAD and 3D printing), Industrial Internet of Things (IIoT), cloud computing, Smart Manufacturing Execution Systems (SMESs), smart factories, Digital Twins, wearables, Big Data & Analytics, and immersive technologies.
What are some of the best innovative products of the information (contemporary) age?
The most famous innovative products to emerge after 1945 include the transistor (1947), integrated circuit (1959), the Internet (1969), microprocessor (1971), mobile phone (1973), computer (1975), 3D printing (1983), semiconductors (1986), smartphone (2007), and VR headsets (2012).